Hubo un día en el que un pequeño objeto metálico, con forma de curva sencilla, recorrió más de 400 kilómetros para volver a casa. No venía de una fábrica ni de un laboratorio terrestre. Venía directamente del espacio. Creado a bordo de la Estación Espacial Internacional (ISS), este pequeño fragmento de acero inoxidable ha hecho historia al convertirse en el primer metal fabricado fuera del planeta que regresa a la Tierra.
Puede que a primera vista no parezca gran cosa: apenas pesa unos gramos y cabe en la palma de una mano. Pero detrás de este modesto objeto hay años de investigación, ingeniería de vanguardia y un objetivo ambicioso: permitir que los astronautas fabriquen en el espacio las herramientas y piezas que necesiten, sin tener que esperar a un costoso envío desde la Tierra. Una idea que parecía sacada de la ciencia ficción y que hoy empieza a tomar forma.
Hasta ahora, la impresión 3D ya había dado sus primeros pasos en el espacio, pero siempre utilizando plástico. Las impresoras de polímeros llevan tiempo siendo una herramienta útil a bordo de la ISS, permitiendo crear objetos ligeros para usos sencillos. Pero imprimir en metal es un desafío de otra magnitud.
El motivo principal es que el metal necesita temperaturas muchísimo más altas para fundirse y solidificarse. En el caso del acero inoxidable, se alcanza una temperatura de unos 1400 °C. Crear y controlar un proceso así dentro de una nave habitada por seres humanos es un reto enorme. Por eso, el desarrollo de la primera impresora 3D de metal apta para operar en microgravedad ha sido considerado un hito tecnológico.
Este logro ha sido posible gracias a la colaboración entre la Agencia Espacial Europea (ESA) y la empresa Airbus Defence and Space. El dispositivo, conocido como Metal 3D Printer, fue enviado a la Estación Espacial Internacional en enero de 2024, a bordo de la misión de reabastecimiento Cygnus NG-20. Su destino: el módulo Columbus, un laboratorio europeo dentro de la ISS.
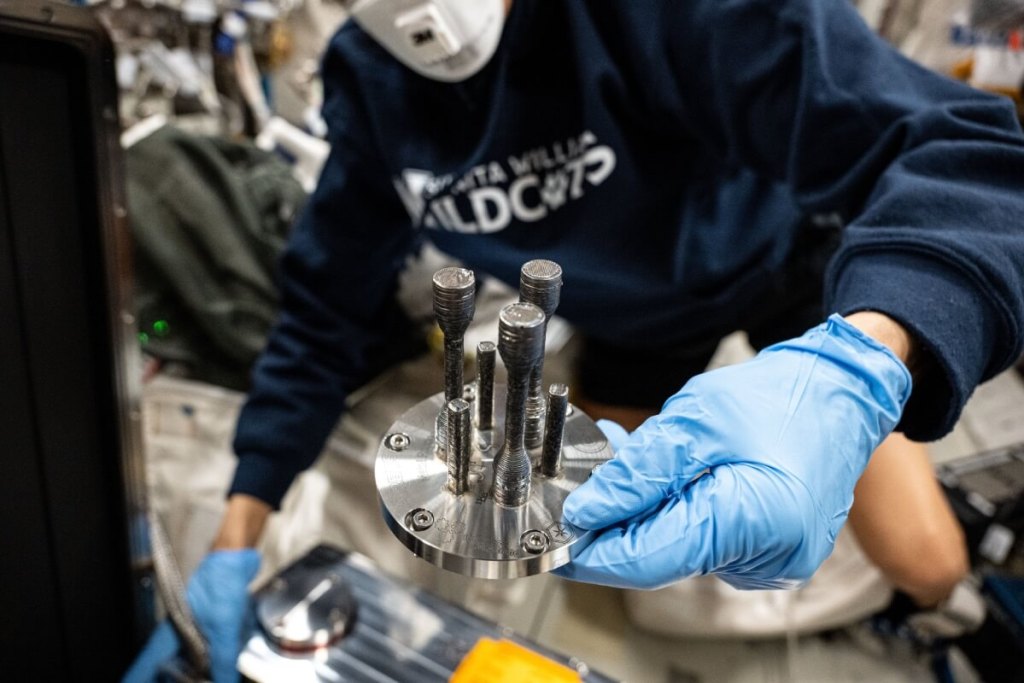
El funcionamiento de esta impresora es tan espectacular como complejo. En lugar de filamentos de plástico, utiliza un alambre de acero inoxidable, un material elegido por su resistencia a la corrosión y su solidez. Este alambre se va alimentando dentro de una pequeña piscina de metal fundido, que se crea al aplicar un láser de alta potencia.
Este láser es hasta un millón de veces más potente que un puntero láser convencional. El calor generado es suficiente para fundir el acero y permitir que se deposite capa a capa, creando la forma deseada. El control del proceso es absolutamente preciso, ya que el menor fallo podría generar partículas peligrosas o dañar la estructura interna de la ISS.
Además, todo el sistema está encerrado en un compartimento sellado. Antes de empezar a imprimir, el oxígeno se elimina de la cámara y se sustituye por nitrógeno. Esto es fundamental porque el acero fundido, en contacto con oxígeno, podría oxidarse rápidamente y comprometer la calidad del objeto creado.

Qué se imprimió y por qué es tan importante
El primer objeto que se imprimió fue una curva en forma de “S”, una figura sencilla pero crucial para comprobar que el sistema funcionaba correctamente. Más adelante, el equipo de la ESA se atrevió con formas más complejas, aunque todas de tamaño reducido, de menos de 250 gramos cada una y más pequeñas que una lata de refresco.
Estos objetos no fueron elegidos al azar. Su diseño buscaba analizar cómo afecta la microgravedad al proceso de impresión: cómo se comporta el metal fundido, cómo se solidifica, qué propiedades tiene el resultado final. Todos estos datos son esenciales para avanzar en futuras aplicaciones.
Una vez impresas las piezas, el astronauta Andreas Mogensen, encargado de operar el sistema, las empaquetó cuidadosamente para su regreso a la Tierra. El análisis de estas muestras, en comparación con piezas idénticas impresas en la Tierra, permitirá entender mejor las diferencias y las posibles ventajas o desventajas de imprimir metal en el espacio.
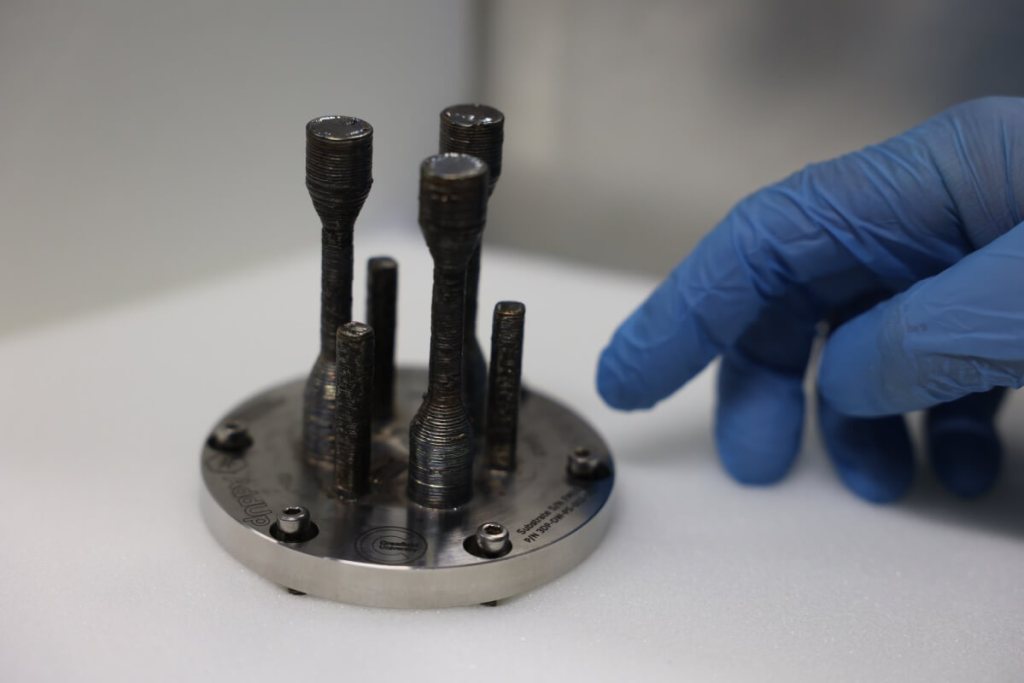
Qué significa este logro para el futuro de las misiones espaciales
El principal beneficio de poder imprimir en metal en el espacio es evidente: la autosuficiencia de las tripulaciones. Hasta ahora, cualquier herramienta o pieza de repuesto tenía que ser enviada desde la Tierra. Este proceso no solo es lento, sino también extremadamente caro.
Con una impresora 3D de metal, los astronautas podrían fabricar directamente en órbita herramientas específicas, adaptadas a situaciones imprevistas, o incluso piezas de recambio para equipos dañados. Esto resulta aún más crucial cuando se piensa en futuras misiones de larga duración, como las que se plantean hacia la Luna o Marte.
En estos destinos, estar a días o incluso meses de distancia de un envío terrestre hace indispensable contar con recursos propios. La fabricación in situ puede marcar la diferencia entre el éxito y el fracaso de una misión.
Además, la ESA ya contempla posibilidades aún más ambiciosas. Una de ellas es crear una economía circular en el espacio, donde los materiales procedentes de satélites antiguos o de estructuras en desuso puedan reciclarse y transformarse en nuevas piezas gracias a la impresión 3D de metal.
Un paso más hacia la fabricación de infraestructuras en el espacio
Este primer experimento con impresión de metal en la ISS es solo el principio. Los ingenieros de la ESA y Airbus tienen en mente desarrollar tecnologías que permitan imprimir no solo pequeñas piezas, sino estructuras más grandes y complejas.
Esto podría incluir desde antenas y paneles hasta partes de hábitats espaciales o vehículos. Imprimir estructuras directamente en el espacio reduciría enormemente el coste y la dificultad de lanzarlas desde la Tierra. También permitiría diseños optimizados para las condiciones espaciales, imposibles de fabricar en fábricas terrestres.
Otro de los campos en los que se espera que esta tecnología tenga un papel importante es en la reparación y el mantenimiento de grandes infraestructuras en órbita. La posibilidad de fabricar y sustituir piezas metálicas in situabre la puerta a un espacio más sostenible y operativo a largo plazo.
La primera pieza vuelve a casa: análisis y próximos pasos
El pequeño fragmento metálico que ha vuelto a la Tierra ya se encuentra en las instalaciones de la ESA en Países Bajos, concretamente en el centro ESTEC. Allí, los investigadores están realizando análisis detallados, estudiando desde la estructura microscópica del material hasta sus propiedades térmicas y mecánicas.
Otra de las piezas impresas se enviará a la Universidad Técnica de Dinamarca, donde se analizará su comportamiento térmico, un factor clave para aplicaciones como las antenas espaciales.
Estos análisis no solo permitirán mejorar la tecnología de impresión 3D en el espacio, sino también explorar nuevas aplicaciones en sectores industriales terrestres. Porque lo que se aprende en el espacio no siempre se queda en el espacio.
Como explicaba Thomas Rohr, responsable de materiales y procesos de la ESA: “Este proyecto demuestra que la fabricación de metales en microgravedad es posible y abre el camino a nuevas formas de construir infraestructuras más allá de los límites de la Tierra”.
Referencias
Cortesía de Muy Interesante
Dejanos un comentario: